ES&H Manual | |
Chapter 6230 Electrical Safety Manual- Appendices | |
Purpose This chapter and its associated appendices are written to outline Jefferson Lab's programs and procedures to satisfy the requirements of 10 CFR 851-Worker Safety & Health Program.
ScopeAll work on electronic equipment is classified according to equipment Class and work Mode. Work performed at Jefferson Lab within these Class and Mode configurations is done in accordance with the programs and procedures. Equipment defined as AC Utilization Equipment is also covered. NOTE: Work performed on building services electrical equipment is covered in ES&H Manual Chapter 6220 AC Electrical Equipment Safe Work Policy. Work performed on electronic equipment exposes workers to potential electrical hazards that may result in serious injury or death. These hazards include; shock, arc flash, arc blast and other physical injury due to reactions to unexpected energy release. The program in this chapter defines the training requirements and some basic work rules, based on the equipment Class and the work Mode, which must be followed when doing work on electronic equipment. Worker qualification levels are identified as well as information on the use of work planning and Work Control Documents. Work that is permitted is identified along with some work that is not allowed.
|
|
Appendices:
T1 Determining Equipment Class and Work Modes
The work rules for electronic equipment are dependent on both the equipment Class and the work Mode. Training requirements and the necessity for Work Control Documents are determined by an evaluation of the Class and Mode. The Class, Mode, and minimum work rules are determined based on the information in ES&H Manual Chapter 6230 Appendix T1 Determining Equipment Class and Work Modes.
T2 Work Planning and Execution for Electronic Equipment Safety
The work rules for electronic equipment are dependent on both equipment Class and work Mode. Workers must determine the training requirements and applicable work rules once the equipment Class and work Mode are identified. The required steps for turning a work assignment into a work plan can then be determined. ES&H Manual Chapter 6230 Appendix T2 Work Planning and Execution for Electronic Equipment Safety provides an outline for determining the steps necessary to plan work on this type of equipment, identify the hazards, and develop work controls.
Supplemental Material: NFPA 70E (2015) – Standards for Electrical Safety in the Workplace NFPA 70 (2017) – National Electric Code OSHA Regulation 29 CFR 1910 and 29 CFR 1926 DOE Electrical Safety Handbook |
Responsibilities:
Management authority may be delegated to a task qualified Jefferson Lab employee at the discretion of the responsible manager. Anyone at Jefferson Lab
Qualified Electronic/Electric Worker (QEW)
Qualified Electrical Inspector
Supervisor/Technical Representative (TR)/Sponsor:
Facilities Management Electrical Engineer
Electrical Safety Engineer
Electrical Authority Having Jurisdiction
Associate Director/Division Head
Laboratory Director
|
Expectations:
The hazard exposure and consequent risks are determined by the equipment Class and the work Mode (see ES&H Manual Chapter 6230 Appendix T1 Determining Equipment Class and Work Modes). A graded approach, based on Classes and Modes, is used to determine training requirements and worker qualifications required for performing work on electronic equipment. Listed below are the minimum requirements. Supervisors, or other organizational groups, may specify more stringent rules. Mode 1 Work Only Equipment fully de-energized - Non-Electrical Work
Workers who are not Qualified Electrical Workers may work on electronic equipment (e.g. – mechanical technician can change magnet cooling hoses; a vacuum technician can change a pump motor), if they comply with the following rules:
REMINDER: A zero voltage test, as in the "Try" portion of LTT, is a Mode 2 operation, when a Voltage Verification Unit (VVU) is not present, and constitutes exposure – see ES&H Manual Chapter 6230 Appendix T1 Determining Equipment Class and Work Mode) Mode 2 and 3 Work on Class 1 Equipment
Class 1 equipment is considered low hazard and is a low risk for injury. As a result, training requirements are less stringent. Work is allowed at all work Modes on Class 1 equipment if the worker has the following training and requirements:
Mode 2 Work on Class 2 and Class 3 Equipment
Class 2 and Class 3 equipment are considered medium and high hazard respectively. Mode 2 involves testing and measuring of energized equipment with normal protective barriers removed and potentially bypassed interlocks. Workers performing Mode 2 work are exposed to operating voltages and currents that can cause serious injury or death. As a consequence, the knowledge and training required to perform Mode 2 work is more stringent.
NOTE: The "Try" process in the LTT lockout procedure is considered a Mode 2 operation, if protective barriers (covers, doors, etc.) are removed in order to take a measurement. Use of an installed VVU is not considered a Mode 2 operation. The following is required for Mode 2 work on Class 2 and Class 3 equipment:
Mode 3 Work on Class 2 and Class 3 Equipment
Mode 3 work is defined as manipulative operations on an energized circuit. This may include re-wiring or replacing components in an energized piece of equipment. In general this is not usually necessary for any reason in electronic equipment at Jefferson Lab. In the event that Mode 3 work is required on Class 2 or Class 3 equipment special rules apply:
|
|
Document Control:
|
|
This document is controlled as an on-line file. It may be printed but the print copy is not a controlled document. It is the user's responsibility to ensure that the document is the same revision as the current on line file. . |
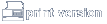